.jpg)
In this case study, integrated palm oil player IOI Corporation Berhad explains its holistic approach towards waste management and how it is rooted in the company’s commitment to circularity as a pathway towards achieving net-zero carbon emissions by 2040.
Industrial waste is often treated in most sectors as a disposal challenge, but agribusinesses have long leveraged on the organic by-products of their crops as valuable resources. Malaysia’s palm oil companies are no exception, using regenerative agricultural techniques such as mulching and organic composting to enrich the soil and improve yields.
Beyond its economic and environmental benefits, improved waste management is also crucial towards achieving circularity, which in turn plays a part in supporting climate action. At IOI Corporation Berhad, circularity and waste management are part of the integrated palm oil player’s holistic response to climate change, which culminates in its broader goal of achieving net-zero carbon intensity by 2040.
Embedding circularity within IOI’s operations follows from its overarching strategies to combat climate change. This involves reducing its climate impact to achieve its net-zero goals and promoting climate action via innovation, improved efficiencies and supporting action throughout its upstream and downstream operations.
Identifying Circularity as A Material Matter
In 2023, IOI identified waste management and the circular economy as one of four new “sustainability material matters”, which are issues that may significantly impact the group’s stakeholders and its business. IOI’s top 10 sustainability material matters were selected following a stringent internal process – from selecting sustainability concerns faced in IOI's operations, determining their impact on internal and external stakeholders, and ensuring the final selection was validated by internal governance parties. [See graph]
To IOI, circularity and waste management matter because irresponsible production and consumption can overexploit natural resources, placing biodiversity and future generations at risk. The company adopts the 7Rs of circularity – Rethink, Repurpose, Reduce, Reuse, Recycle, Repair and Recover – to reduce its greenhouse gas emissions and other environmental impacts. It also disposes of all hazardous wastes following local laws and regulations.
Practicing the 7Rs has helped the company create closed-loop systems by improving waste management and resource efficiency and are enablers for IOI to align closely to the United Nations’ Sustainable Development Goal 12 of Responsible Consumption and Production.
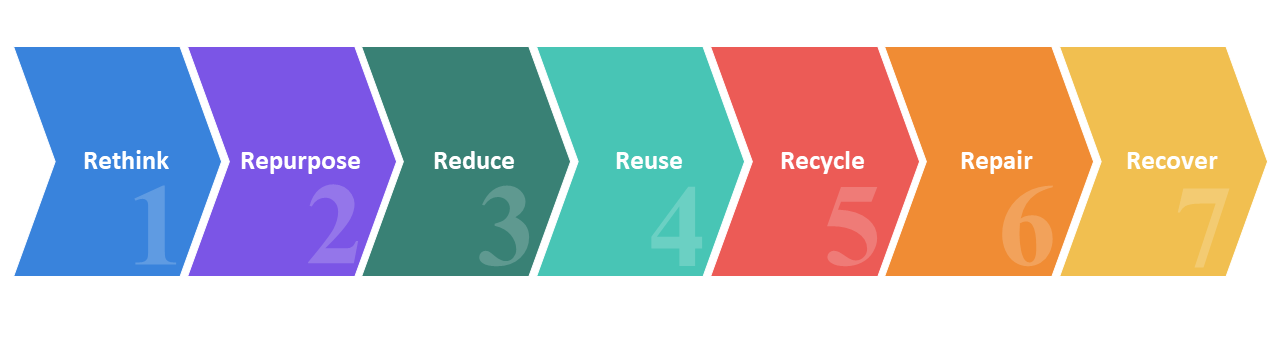
Circularity In Action
Developing and executing the 7Rs at IOI begins with ensuring that stakeholders understand the principles of circularity. The firm practices ‘rethinking’ by instilling awareness among employees through talks and trainings such as zero waste, biodiversity through urban farming, and converting waste to treasure, it told Bursa Sustain.
Rethinking the opportunities associated with oil palm-related waste has led to adoption of the subsequent ‘R’s. For example, IOI reimagined the ways in which felled oil palm trunks (OPT) could be repurposed to become a new material.
From old trunks to new wood products
Oil palm trees are typically felled for replanting when they have grown too tall to harvest or no longer bear viable fruits. While felled palms are often allowed to decay naturally and in some cases are eaten by pygmy elephants, decaying oil palm trunks (OPT) release greenhouse gases and can potentially attract pests and diseases due to their slow decomposition.
Given that OPT is the most abundant biomass source at IOI, the group seized the opportunity to repurpose the felled OPT on its plantations into commercially sustainable, eco-friendly wood panels for the furniture and building industries.
IOI Palm Wood Sdn Bhd was therefore established to commercially produce engineered wood panels sustainably from OPT waste. Repurposing OPT waste into lumber is meant to lock in the carbon emissions, which would otherwise be released into the atmosphere. Furthermore, palm wood can serve as a substitute for traditional timber, easing the pressure on felling natural forests and preserving habitats and ecosystems.
The IOI Palmwood manufacturing facility is the first in Malaysia, using customised European technology to repurpose the OPT. It has the capacity to produce up to 80,000 cubic metres of palm-based wood products per annum, and its premium products are sold under the commercial brand OnCore. These products include premium grade kiln dried palm lumber, blockboards and palm wood panels, all of which adhere to international quality and safety standards.
All OnCore products are treated to last for more than a decade which extends their role in emissions storage. The end-of-life OnCore products can also be upcycled or used as bioenergy. This not only expands the circularity potential of this product, but also further enhances the commercial potential of the venture.
To reduce and reuse wastage on its plantations, IOI employs a combination of regenerative and precision agriculture. Regenerative agriculture involves the use of organic compost – cycling organic waste back as mulch onto the land and weeding manually to limit soil disturbance1. Precision agriculture employs a combination of technologies and innovations to optimise yields, including the use of machines on plantations to transport and evacuate fresh fruit bunches.
Overall, both regenerative and precision techniques have resulted in a 30 per cent increase in IOI’s worker-to-hectare ratio by increasing productivity. These techniques have also directly reduced IOI’s greenhouse gas emissions, with regenerative agriculture in particular resulting in lower and more precise use of chemical fertilisers and pesticides2.
Another significant source of greenhouse gas emissions for IOI is the methane released by the waste palm oil mill effluent (POME) from the company’s mills. This methane has been captured and repurposed as a renewable energy source since 2013. IOI currently runs 10 methane capture plants across its mills that produce about 45 million cubic metres of biogas, which is used to fuel boilers and electricity generation. Using captured methane as fuel also means that biomass which was previously burned in the boilers can be used for other purposes such as mulching, fertiliser and activated carbon.
IOI’s practice of its 7Rs also extend to its treatment of wastewater, particularly via the recycling and reusing of wastewater throughout its operations. Effluent water from the company’s refineries is treated according to local regulations before being recycled and reused. The group’s oleochemical facilities follow a similar process, treated effluents are cycled back into its cooling towers.
The group practices the final two ‘R’s, ‘repair’ and ‘recover’, by repairing the machineries in its mills and factories, as well as recovering the parts for other uses. On the social front, IOI recovers and donates its older office computers to communities in need, such as schools and welfare homes.
Improved Recycling Rates
As a result of IOI’s implementation of the 7Rs, its it achieved a 95 per cent recycling rate of non-hazardous waste in its 2023 financial year, a 13 per cent increase compared to the year before. The bulk of this was attributed to its plantation arm, which recycled and reused 97 per cent of non-hazardous waste, mostly comprised of biomass in the form of empty fruit bunches and POME.
Meanwhile, the company’s refinery business also recycled over 97 per cent of its non-hazardous waste, mainly by repurposing biomass from treated palm oil refinery effluent and ashes from refining operations as fertiliser.
Moreover, IOI’s oleochemicals reduced their waste disposal volumes by repurposing soap scraps into hygienic scented soaps in collaboration with third parties, while palm oil sludge is being repurposed as a raw material for the cement industry.
These outcomes demonstrate that the implementation of the 7Rs have helped the group to minimise its environmental impact while unlocking new opportunities for value creation. IOI's success in reducing waste and improving resource efficiency highlights the business case for implementing climate-responsive approaches to waste management and is a testament to the benefits of applied circularity.